This example shows how to automatically tune a PID Controller block using PID Tuner.
Introduction of the PID Tuner
PID Tuner provides a fast and widely applicable single-loop PID tuning method for the Simulink® PID Controller blocks. With this method, you can tune PID controller parameters to achieve a robust design with the desired response time.
These settings are rough, assume proper control loop design, ideal or series algorithm and do not apply to all controllers. Use Expertune's PID Loop Optimizer to find the proper PID settings for your process and controller. (From Process Control Systems (Shinskey) p.99 and Tuning and Control Loop Performance. Simulink Control Design provides several approaches to tuning Simulink blocks, such as Transfer Fcn and PID Controller blocks. Introduction to Model-Based PID Tuning in Simulink. Use PID Tuner for interactive tuning of PID gains in a Simulink model containing a PID Controller or PID Controller (2DOF) block. The process of finding these values is referred to as “tuning.” When a PID controller is tuned optimally, the device minimizes deviation from the set point, and responds to disturbances or set point changes quickly but with minimal overshoot. This White Paper from OMEGA Engineering discusses how to tune. A COMPARISON AND EVALUATION OF COMMON PID TUNING METHODS by JUSTIN YOUNEY B.S. Rochester Institute of Technology A thesis submitted in partial fulfillment of the requirements for the degree of Master of Science in the School of Electrical Engineering and Computer Science in the College of Engineering and Computer Science.
A typical design workflow with the PID Tuner involves the following tasks:
(1) Launch the PID Tuner. When launching, the software automatically computes a linear plant model from the Simulink model and designs an initial controller.
May 30, 2015 This work is directed towards the design, development and implementation of an auto-tuning Proportional Integral Derivative (PID) controller for heat exchanger present in forced circulation evaporator pilot plant and boiler and heat exchanger pilot plant. Jul 24, 2018 PID tuning can be thought of in two ways: Adjusting the three path gains (Kp, Ki, and Kd), or placing two moveable zeros and adjusting the loop gain to get the desired response. This video shows.
(2) Tune the controller in the PID Tuner by manually adjusting design criteria in two design modes. The tuner computes PID parameters that robustly stabilize the system.
(3) Export the parameters of the designed controller back to the PID Controller block and verify controller performance in Simulink.
Open the Model
Open the engine speed control model with PID Controller block and take a few moments to explore it.
Design Overview
In this example, you design a PI controller in an engine speed control loop. The goal of the design is to track the reference signal from a Simulink step block scdspeedctrlpidblock/Speed Reference
. The design requirement are:
Settling time under 5 seconds
Zero steady-state error to the step reference input.
In this example, you stabilize the feedback loop and achieve good reference tracking performance by designing the PI controller scdspeedctrl/PID Controller
in the PID Tuner.
Open PID Tuner
To launch the PID Tuner, double-click the PID Controller block to open its block dialog. In the Main tab, click Tune.
Initial PID Design
When the PID Tuner launches, the software computes a linearized plant model seen by the controller. The software automatically identifies the plant input and output, and uses the current operating point for the linearization. The plant can have any order and can have time delays.
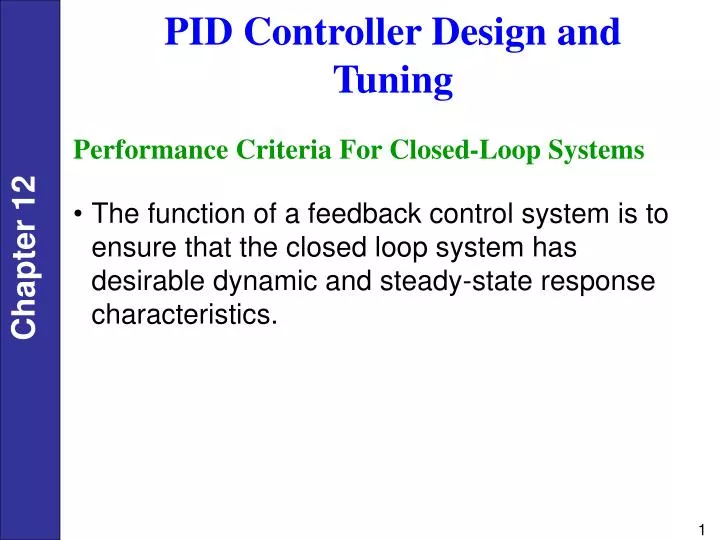
The PID Tuner computes an initial PI controller to achieve a reasonable tradeoff between performance and robustness. By default, step reference tracking performance displays in the plot.
The following figure shows the PID Tuner dialog with the initial design:
Display PID Parameters
Click Show parameters to view controller parameters P and I, and a set of performance and robustness measurements. In this example, the initial PI controller design gives a settling time of 2 seconds, which meets the requirement.
Adjust PID Design in PID Tuner
The overshoot of the reference tracking response is about 7.5 percent. Since we still have some room before reaching the settling time limit, you could reduce the overshoot by increasing the response time. Move the response time slider to the left to increase the closed loop response time. Notice that when you adjust response time, the response plot and the controller parameters and performance measurements update.
The following figure shows an adjusted PID design with an overshoot of zero and a settling time of 4 seconds. The designed controller effectively becomes an integral-only controller.
Complete PID Design with Performance Trade-Off
In order to achieve zero overshoot while reducing the settling time below 2 seconds, you need to take advantage of both sliders. You need to make control response faster to reduce the settling time and increase the robustness to reduce the overshoot. For example, you can reduce the response time from 3.4 to 1.5 seconds and increase robustness from 0.6 to 0.72.
The following figure shows the closed-loop response with these settings:
Write Tuned Parameters to PID Controller Block
After you are happy with the controller performance on the linear plant model, you can test the design on the nonlinear model. To do this, click Update Block in the PID Tuner. This action writes the parameters back to the PID Controller block in the Simulink model.
The following figure shows the updated PID Controller block dialog:
Completed Design
The following figure shows the response of the closed-loop system:
The response shows that the new controller meets all the design requirements.
You can also use the Control System Designer to design the PID Controller block, when the PID Controller block belongs to a multi-loop design task. See the example Single Loop Feedback/Prefilter Compensator Design.
See Also
What Are Pid In Performance Auto Tuning Shops
Related Topics
The Ziegler–Nichols tuning method is a heuristic method of tuning a PID controller. It was developed by John G. Ziegler and Nathaniel B. Nichols. It is performed by setting the I (integral) and D (derivative) gains to zero. The 'P' (proportional) gain, is then increased (from zero) until it reaches the ultimate gain, which is the largest gain at which the output of the control loop has stable and consistent oscillations; higher gains than the ultimate gain have diverging oscillation. and the oscillation period are then used to set the P, I, and D gains depending on the type of controller used and behaviour desired:
Control Type | |||||
---|---|---|---|---|---|
P | – | – | – | – | |
PI | – | – | |||
PD | – | – | |||
classic PID[2] | |||||
Pessen Integral Rule[2] | |||||
some overshoot[2] | |||||
no overshoot[2] |
The ultimate gain is defined as 1/M, where M = the amplitude ratio, and .
These 3 parameters are used to establish the correction from the error via the equation:
which has the following transfer function relationship between error and controller output:
Evaluation[edit]
The Ziegler–Nichols tuning (represented by the 'Classic PID' equations in the table above) creates a 'quarter wave decay'. This is an acceptable result for some purposes, but not optimal for all applications.
This tuning rule is meant to give PID loops best disturbance rejection.[2]
It yields an aggressive gain and overshoot[2] – some applications wish to instead minimize or eliminate overshoot, and for these this method is inappropriate. In this case, the equations from the row labelled 'no overshoot' can be used to compute appropriate controller gains.
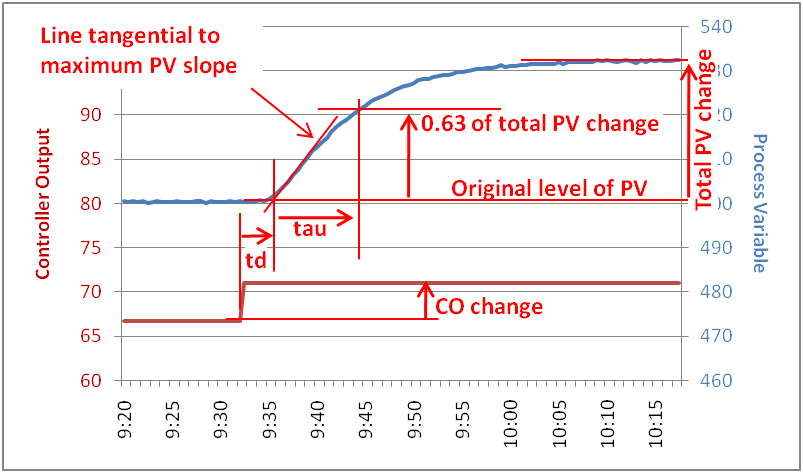
References[edit]
- ^Ziegler, J.G & Nichols, N. B. (1942). 'Optimum settings for automatic controllers'(PDF). Transactions of the ASME. 64: 759–768.Cite journal requires
|journal=
(help) - ^ abcdefZiegler–Nichols Tuning Rules for PID, Microstar Laboratories
- Bequette, B. Wayne. Process Control: Modeling, Design, and Simulation. Prentice Hall PTR, 2010. [1]
- Co, Tomas; Michigan Technological University (February 13, 2004). 'Ziegler–Nichols Closed Loop Tuning'. Retrieved 2007-06-24.
Comments are closed.